Back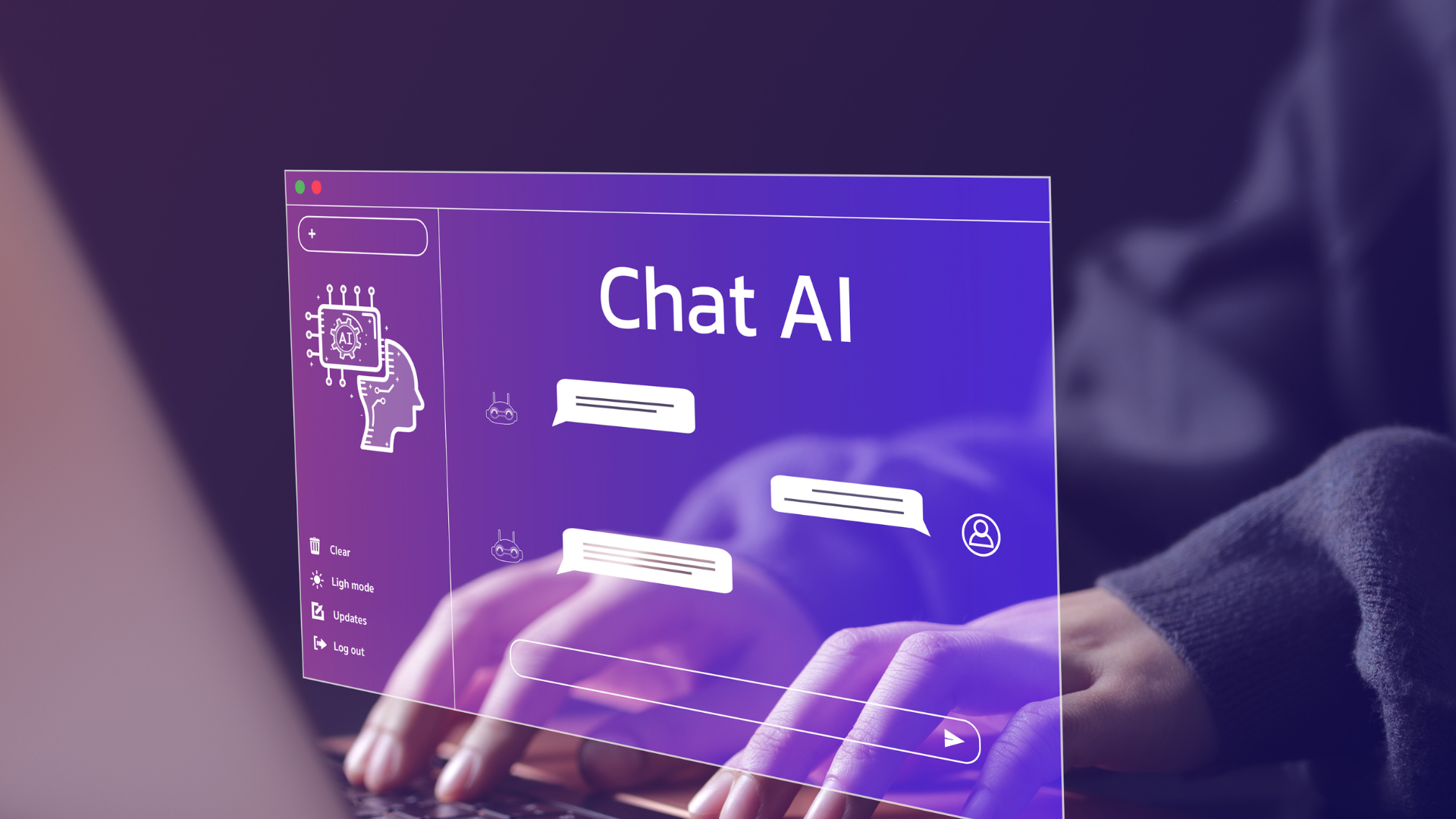
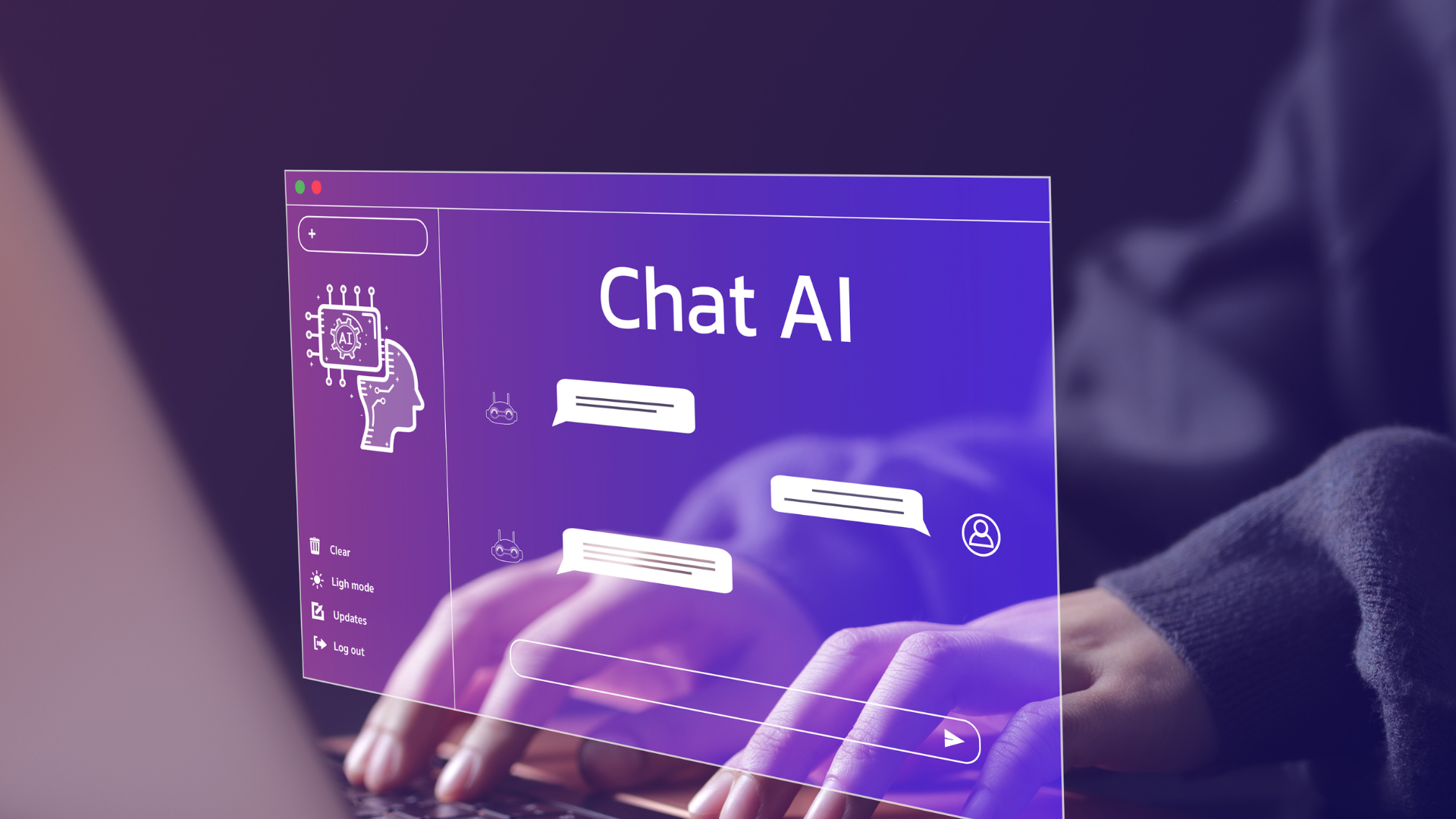
GOODS QUALITY CONTROL CHATBOT: ARTIFICIAL INTELLIGENCE ON GUARD OF CONSUMERS AND BUSINESS
10 April 2024
SERVOLUX HAS BEEN IMPLEMENTING THE MOST ADVANCED TECHNOLOGY TO ENSURE CONTINUOUS AND EFFICIENT MONITORING OF PRODUCT COMPLIANCE WITH ALL NECESSARY REQUIREMENTS, INCLUDING IN SHOPPING SPACES.
For instance, the Goods Quality Control Chatbot project developed specifically for the product segment of goods to be sold on the Belarusian and Russian market was implemented after testing in November 2023.
How it works The Goods Quality Control Chatbot is a digital tool for internal use, with access to the interface being limited to Servolux employees only. The project represents a controlled program with detailed requirements for each specific type of product and its packaging in terms of appearance and contents. Marketing employees receive monthly assignments using the randomizer to conduct product research in various chain stores both in the Republic of Belarus and the Russian Federation. Class A shopping spaces are common objects of research. Random assignments ensure an unbiased approach to their fulfilment.
Products in shopping spaces are analyzed visually and photographed, with subsequent photo uploading to the Goods Quality Control Chatbot, by company employees. Further, the uploaded photo is compared with the requirements given in the product data sheets by specialists using the program algorithm. The chatbot evaluates the fulfilment of numerous requirements that ensure an objective identification and classification of nonconformities. The specifications and esthetic parameters of packaging, product appearance and volume, presence or absence of foreign matter, the product storage conditions on shelves and many more are registered based on electronic product data sheets only (original development by Servolux). The subjective evaluation is excluded.
What results does it yield? Data results obtained via the chatbot are generated as an automatic report and analyzed during the Quality Days. These are monthly meetings of company brand managers and production site heads. Report data are examined, the reasons for the nonconformities are identified and the decision concerning the methods of their elimination is made by the specialists collectively during the Quality Days. Fifty-seven percent of the nonconformities identified using the chatbot were eliminated based on the Q1 2024 data. Also, the improper product storage in retail facilities was frequently reported as the reason for the nonconformities.
Research findings obtained via the Goods Quality Control Chatbot allow improving the production process and enhancing monitoring of the transportation and storage conditions. Hence, it allows making Servolux products even more attractive to consumers, which has a positive effect on the company performance.